Extending Equipment Oil Life
Date: Friday, November 30, 2012
Oil life can be extended indefinitely… FACT or MYTH ??
Do we really need to change oil by the calendar or the odometer ??
Does oil really wear out ??
For years the accepted practice has been to change oil in equipment on a pre-set scheduled basis regardless of whether the oil is spent. Changing oil and disposing of used oil is a major cost to industry and the environment and the old traditional practices can no longer be considered sustainable or practical.
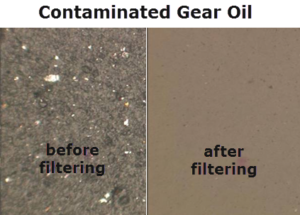
Mostly used oil is simply loaded with contaminants such as dirt particles, wear metals, water and gases, while the oil remains within specifications and suitable for continued use. Acids can be prevented from developing simply by keeping the oil ‘dry’ as being aqueous, acids will only form in the presence of water.
If the contaminants can be adequately removed without affecting the additives, there is no reason why oils cannot remain in service.
Regular oil testing will let you know when your oil needs servicing and enables you to extend the oil life in a safe manner without risk to expensive equipment. Oil condition is easily monitored with simple laboratory tests, providing regular checks on the quality of the oil. A pro-active Oil Analysis program is integral to any extended oil life regime.
Cleaning the oil with a centrifuge and vacuum dehydration oil filtration system is the most economical and efficient method of extending the oil life. Using this type of oil filtration system it is possible to clean all grades of oil and achieve higher cleanliness levels than with pore membrane filter systems. The many benefits of oil filtration for extended oil life include:
- Reduced amounts of waste oil
- Reduction or elimination of waste oil removal from site
- Reduction in the volumes of new oil purchased
- Reduced service downtime
- Reduced environmental impact
- Substantial overall savings in Lubrication expenditure
Doubling your oil life halves your lubricant cost. Even when you do change your oil, it does not guarantee complete removal of contamination as it doesn’t flush out the contaminants left in the hoses and plumbing of equipment.
Keeping your lubricant in perfect operating condition through using scheduled oil analysis combined with oil filtration will reduce downtime and extend machine life. It is pro-active rather than re-active and extremely cost effective.
Oil is a valuable resource and a huge part of any maintenance budget…… Look after it, maintain it and it will serve you better for longer. Contact Clean Oil Services to more information.
Category: Oil Analysis